
National Science Centre (NCN) supports fundamental research by funding research projects carried out by individual researchers and research teams, both on the domestic and international level, as well as doctoral fellowships and post-doctoral internships. NCN announces calls for proposals four times a year. The NCN grantee must be employed at a Polish host institution.
In March 2018, National Science Centre has approved and subsidized two projects from IPPT PAN:
1. Advanced modelling and optimization of mechanical metamaterials' structures for smart control of vibrations (SONATA BIS - PhD holder grants)
Project coordinator: Bartłomiej Dyniewicz, Ph.D., Dr. Habil.
Growing requirement for modern structures to improve the safety, comfort and durability of mechanical systems makes it necessary to look for new solutions that significantly reduce harmful vibrations, while ensuring adequate strength of the proposed solution. As a consequence, adaptation structures automatically adapting to the new conditions become the subject of intense research for a long time. Properly designed structures allow for significant improvement of the dynamic properties of the systems, compared to their passive equivalents. Executive elements of such solutions are smart materials that allow to quickly change the rheological parameters. Engineering practice proves that the currently available smart materials have significant disadvantages that limit their potential use in practice. It is most commonly excessive weight, but most of all the need of use additional complex equipment to enable modification of parameters. The main goal of the project is to develop a group of intelligent lightweight materials used in the structural dynamics, which will be characterized by autonomous operation. The operation requirements should fulfilled mechanical metamaterials, which dynamic properties determine their geometric structure rather than the composition of base materials. Through the use of efficient computational tools and modern achievements in the field of additive manufacturing it seems possible to design and produce special prototype metamaterials, which have non-typical functional characteristics unexplored so far. Determination of the geometric structures of metamaterials mimics investigated earlier semi-active control strategies requires the development of fast and reliable numerical tools. In the inverse problem, the simplest possible structures implementing the elastic properties will be searched. In order to find the appropriate structure with the best rate of energy dissipation, an optimization problem will be formulated. Based on computer models, the custom tailored metamaterial will be fabricated in the 3D printing processes. The efficacy of the designed hollow material configuration will be evaluated experimentally. It is assumed that the proposed self-activating metamaterials outperform the commercially explored solutions and at the same time will remain cost-effective and easy to manufacture. In the future, developed within the project computational environment should allow to design geometric structures of metamaterials with established bistable characteristics on request, for specific applications. Developed mechanical metamaterials should revolutionize the semi-active vibration control in many practical applications. They will serve to build safer structures and improve the functionality of the existing ones. This will translate into tangible benefits for society in the form of reducing the loss of human and material resources.
2. Adaptive distributed vibration control of modular structures (SONATA - PhD holder grants)
Project coordinator: Dominik Pisarski, Ph.D.
Over the last decade, decentralization has emerged as a major trend in the field of control systems. Growing interest in this control concept derives from functionality of modern devices that can be perceived as compact modules since they are fully equipped with sensors, actuators, and computing units. Furthermore, the decentralization is a natural response to the demands of systems providing robustness and, above all, ability to adapt to various tasks. In many applications, the design of control system based on the traditional centralized architectures is not only problematic but sometimes also unfeasible. In particular, centralized systems fail in large-scale structures and advanced robotic systems where, due to the complexity of the feedback loops, the computational burden and the amount of instrumentation employed exceed reasonable limits.
The project aims at designing novel collaborative distributed control methods that enable an efficient stabilization of modular structures and machinery. Theoretical work on distributed control will be carried out within the context of semi-active and active actuation of mechanical systems. For several engineering applications, including an active vehicle suspension and a multi-link robot, the performance of the developed controllers will be studied numerically. Experimental works will be performed with uniquely designed platform involving a modular suspension system (Fig. 1) which will confirm the efficiency of the designed control strategies. The project team will focus on designing novel control procedures that fully exploit the potentiality of modern control instrumentation. In addition to that, simplified solutions, involving low-cost control components and readily available semi-active materials, will be retained. The project will be performed in collaboration with scientists of INRIA Rhône-Alpes (Grenoble, France) and Université de Picardie Jules Verne (Amiens, France).
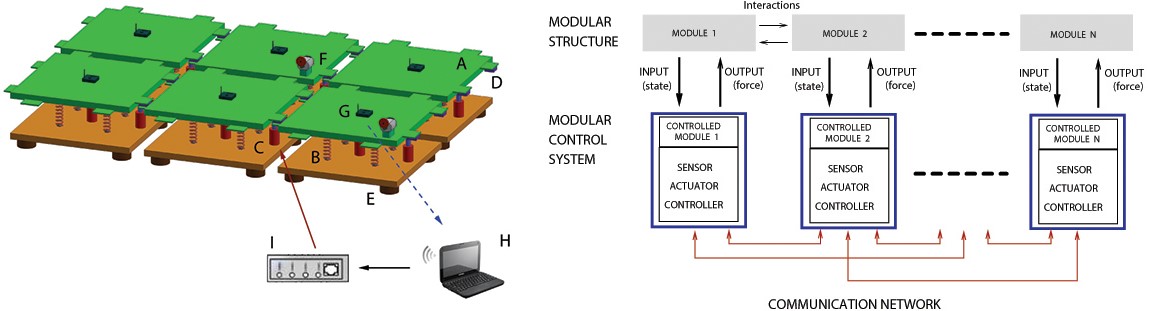
Fig. 1. Modular suspension structure controlled by a distributed system.